Brief description
HG150x150:High frequency welded pipe production line is used to manufacture welded square tube 70x70-150x150mm, thickness 2.0-6.0mm . This line adopt Direct Forming Square technology which have below advantages:
1. In a very short period of time to finish the adjustment of the roller, extreme reduce the roller change time when replace the Products, thus improve the efficiency and reduce the productive cost;
2. Due to the equipment adopts one set of combined mould, producing the different specifications of the tube, only need to adjust,no need to change,the roller savings rate at above 90%,thus reducing the cost of the roller; Need change up roller for final open stand when produce 100x100mm tube.
3. With servo motor adjustment, decreased the input of tools and damage to equipment when change the roll, improve the service life of the equipment.
4. Due to structure of the composite roll,the point contact between the roll and strip instead of the original line contact,reduce the roll wear and improve the service life of roll.
Product parameters
(1)Raw material |
Material Quality |
Q195、Q235B、Q355B、Galvanized Steel、MS、CR、HR |
Mechanical properties |
σb≤500Mpa,σs≤325MPa |
Strip Width |
280-600mm |
Strip Thickness |
2.0-6.0mm |
Coil ID |
Φ508-610mm |
Coil OD |
Φ1200mm-2100mm |
Coil Weight |
10.0T |
(2)Finished Product Size and purpose |
Tube Size |
70x70-150x150mm T:2.0-6.0 mm |
Length |
4-6m |
Application |
Structure |
(3)The working process of the production line |
Raw material (strip)→Coil loading(coil Ramp& coil car)→ Uncoiler→Coil peeler and head straightener→Pinch and leveler→Shear and welder→ Accumulator → passive leveling → Forming →High frequency welding → External scarfing & ironing →Water cooling →Sizing→Turks head→ Milling saw→Conveyor(run out table) →Punching hole →Full auto packing(stacking and strapping) |
(4)Forming type |
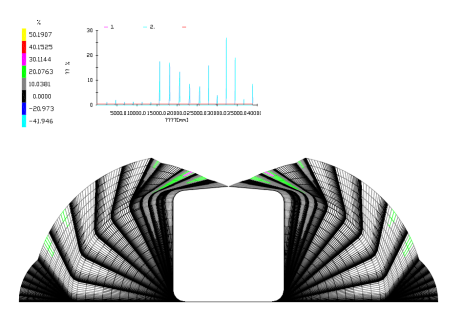 |
(5)This line contain |
Coil conveyor car |
The coil conveyor car is used for make the steel coil from loading position to uncoiler.at the same time loft oil cylinder,so that the steel coil inner hole is accurately set on the cone of uncoiler, after the uncoiler tension, push back to the original position.
|
Uncoiler |
Expansion and cantilever mandrels.
Contains two main parts: main body and the fixed base.
Equipped with pneumatic system to satisfy the needs of expanding, contracting and braking of the mandrels.
Mandrel consists of four-bar linkages that could move radially at the same time.
The four-bar linkages in two groups are fitted on two shafts respectively. Powered by air cylinder, they expand and contract radially.
|
Straight head machine |
This machine is used to open the coil head and smoothly introduce the next device to a smooth machine. The pressure roller on the head is mainly used to press the head of the roll to prevent the scatter roll from scattering, and the shovel is shovel smoothly. The pressure roller rotates under the motor. For the opening machine, it is a help roller. There is a straight head roller, which is mainly the curved pressure of the head of the steel, cooperate with the shovel header, and make it forward along the shovel. The guide roller leads the material into the next process. |
Pinch leveling machine |
The pinching machine is divided into three parts: clamping materials, the flat house roller, and the flattering machine transmission. The five -roller smoothing can change the passing steel through the up and down adjustment of the five rollers to a straight state, and the transmission part of the ingening machine provides motivation for the pinhris roller and the flat roller. |
Automatic shear and welder |
It is used to cut the irregular ends of the strips and then connect the strips by welding. So it can let the line runing without stop when the before coil finish. |
Spiral accumulator |
This machine is between shear welder and host (forming sizing mill) ,use for after a roll of strip steel are used up, before the next roll strip since prepared from uncoiling, shearing and butt welding time to ensure that the host (forming sizing mill) continuous production and store enough strip steel. |
Forming and sizing mill |
Forming & Sizing Mill adopts roller type forming principle and high-frequency induction welding. The strip is fed into the forming machine by the feeding device in the mill and the forming roller continuously rotate and press the strip into the required shape. Due to the skin and the kindred effect, the high-frequency current is concentrated on the weld joint that is heated rapidly and reaches the welding temperature. The tube seam is welded under the pressure of squeeze rollers. The finished welded tube with required size can obtained after the cooling, sizing and primary straightening. |
Cutting saw |
It is used to precisely cut the pipe to length automatically under the condition that the pipe continuously delivered from the mill at high speed. |
600 kw Hifrequency Welder |
Weld the seam |
Runout Transit table |
Transit the finished pipe to the collection table |
|